Lean - 'It's about time'
'The most dangerous kind of waste is the waste we don't recognize' (Shigeo Shingo)
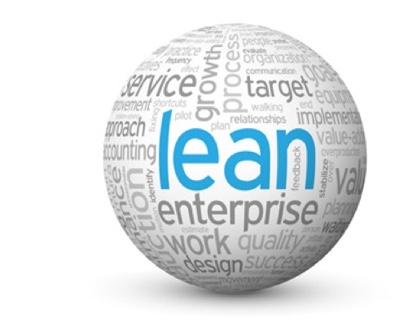
LEAN is about 'saving time in processes by eliminating waste and creating flow'. In practice, only a handful of companies succeed in becoming truly lean. Why is that ?
While Lean is essentially simple, its implementation can be challenging. Many organizations try to 'copy' Toyota or a friendly 'lean' company. Often this is not an undivided success; too little account is taken of their own context and business. Lean is often seen as set of tools to be applied in a department, or sometimes as a short-term cost cutting exercise.
Could it be any other way ? Lean, as with any continuous improvement initiative, means making a strong link with your business strategy. Companies with a different business model, eg product leadership versus cost leadership, benefit from a different application of Lean.
Secondly, Lean is a conscious long-term choice. As if you are at an intersection: the choice is then left or right, not half-right or half-left. Lean means a substantial change and improvement in operational management. That's where the challenge lies. Are we prepared to make that choice?
Lean also means not only having an eye for the financial return in the short-term. We often focus too fast on 'random' and small-scale initiatives because of that financial component. This is a pitfall if Lean is (only) used to save costs. There is then a real chance that Lean will have a negative connotation. As a result, the organization feels less and less involved in every restart of an improvement program. Those who want to continue to reap the benefits of an improvement initiative, often first need to determine the global approach. Financial results will follow with sustained efforts.
Finally, Lean relates to all employees and processes. When Lean is only applied in only one department (eg Production) then 'imbalance' arises in the organization. One will not understand why there is (too) strong focus on cycle times in production, but Lean is less or not applied in the non-production processes (sales, finance, marketing, ...). However, there is a great potential there as well. Involving all departments and processes is a must to make Lean a full success.
Lean has proven its value, and the benefits can be enormous. At least if Lean is rigorously applied in all value streams end-to-end, linked to a long-term vision. These advantages are: committed employees, shorter lead-times, more flexibility in product mix, less space, less stock, higher customer satisfaction, ... As a result, more bottom-line profit.
How can we help?
- Lean Assessment - quantification of the AS IS maturity level
- Lean Transformation - drawing up a roadmap and guiding the transformation
- Value Stream Mapping - identifying value streams, quick wins and opportunities for improvement
- Housekeeping - Perform 5S exercises across departments and processes
- Waste recognition - identification of all types of waste (and how to deal with it)
- Training - Installing Lean competence in your organization
- ...